What Is A Screw Compressor?
Rotary screw compressors are so named due to their method of compressing air. Air enters at the intake end and becomes trapped between two closely meshing helical screws, also known as rotors. As these screws turn, the space between them diminishes, resulting in the compression of the air as it moves through the threads. This process is termed positive displacement.
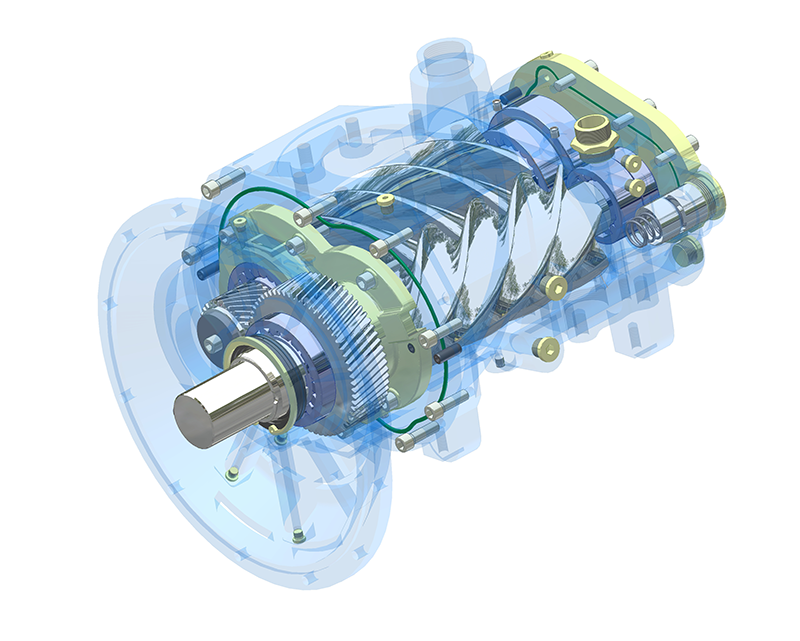
In a dry-running rotary-screw compressor, precise alignment between the male and female rotors is ensured by timing gears, preventing contact that could lead to rapid wear. Conversely, in an oil-flooded rotary-screw compressor, lubricating oil serves a dual purpose: creating a hydraulic seal between the rotors and transferring mechanical energy between them, allowing one rotor to drive the other entirely. Gas enters the compressor at the suction side and progresses through the threads as the screws rotate. The meshing rotors propel the gas through the compressor, and it exits at the end of the screws. The working area, known as the inter-lobe volume between the male and female rotors, diminishes along the length of the rotors from the intake end to the exhaust port, causing compression. At the intake end, the male lobe is considerably smaller than the female lobe, but their relative sizes reverse along the lengths of both rotors until, tangential to the discharge port, the clearance space between each pair of lobes is significantly reduced. This reduction in volume facilitates compression of the gas before it reaches the output manifold.
Here are five benefits of rotary screw compressors:
- Continuous Operation: Screw compressors can maintain continuous airflow and pressurization without the need for frequent start-stop cycles, leading to minimal downtime.
- Easy Maintenance: These compressors have few moving and contacting parts, resulting in reduced wear and tear and longer service intervals, ultimately lowering maintenance costs.
- Powerful Performance: Screw compressors can operate effectively in challenging conditions, offering high airflow rates and performance at extreme temperatures, making them suitable for powering pneumatic tools and heavy equipment.
- Energy Efficiency: With their durable design, screw compressors produce less heat and conserve more energy compared to other models, ensuring minimal loss of capacity over time and lower lifetime costs.
- Low Noise Levels: The compact size and minimal moving parts of screw compressors contribute to their quiet operation, making them suitable for installations where noise levels need to be kept to a minimum.